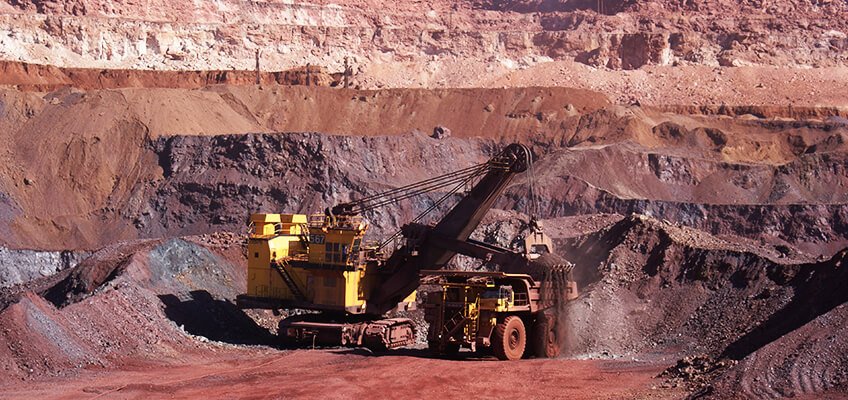
low mineral prices - what to do?
Learn from the best in other industries!
The low minerals prices have forced the mining industry to rethink the viability of its operations. In some cases this has forced companies to divest, or put an operation on care and maintenance. In each case mining companies tend to put a stop to all capital expenditures, but in most cases this only frees up cash on a short term basis whereas it fails to remove costs on a structural basis permanently. This is where successful mining companies have looked to other industries for inspiration. Some of the mining companies who have responded most successfully to the low mineral prices, have done so by copying an industry which is designed to operate with permanently low commodity prices and a need for reliable and cost efficient equipment: The global wind turbine market.
Learn from other mine sites' experiences with the benefits from maintaining their system oil clean:
Case Crusher:
Learn how BHP Billiton, Chile saves 479,600 USD annually on running cost and increased production on their crusher
The global wind turbine market
The global wind turbine market has at least three things in common with the mining industry:
- it is capital intensive (expensive equipment)
- low commodity prices (a permanent given in the wind industry)
- uptime, reliable equipment and throughput are critical to success
Increasing throughput and lowering production costs is possible
For years the mining industry has been all about increasing throughput. A key factor to achieve this is to ensure maximum uptime of equipment; sometimes at a high cost, but as long as the minerals prices are high, then the cost of keeping equipment in operation has had less focus.
With low commodity prices, mining companies now have to reconsider the idea of focusing purely on throughput, but also consider cost per tonnes/ounce/kilo.
Unlike mining, the global power market has always been characterized by low margins on the commodity they sell. This has forced the stakeholders to focus on cost efficient and predictable/reliable production; but also to focus on maximum output. Windfarms are located in isolated areas; and today more and more of these are offshore. Unforeseen breakdowns, too frequent service shutdowns or unreliable equipment are catastrophic in this industry and can literally undermine the profitability of a windfarm.
Like mining, costs associated with a breakdown or a shutdown is extremely high in the wind industry; this is why the wind industry is geared differently than the mining industry, and there are valuable benefits from the wind market which can be applied to the mining industry.
Reduce running costs by 60% and eliminate 75% of service intervals
While mining companies tend to have high operational budgets in order to keep the equipment running, the wind market has focused on measures which keep the equipment in operation cost effectively and reliably. Today the wind industry is working toward two-year service intervals of critical equipment and complete elimination of unforeseen breakdowns. The mining industry are used to monthly - sometimes weekly - service intervals and unforeseen breakdowns or unplanned work orders are industry accepted standards. The interesting thing is that equipment in the wind industry operates under significantly harder loads than it does in the mining industry (in fact more than 60 times the load), and still they manage to keep the equipment in operation for a full year without shutdowns or service intervals.
What to do differently
One of the difference between the two industries is the working environment. While wind has a much higher load, mining equipment operates under much dirtier conditions given the nature of the operation. But this is exactly where some mining companies have been successful; by trying to create similar environments.
Although the operating conditions will never become similar, the mining operations who have implemented technology from the wind industry have seen significant and measurable benefits within a matter of weeks. Enclosed you can read how BHP’s Escondida saved 445,800 USD and eliminated three out of four shutdowns per crusher per year. You can also read how Kinross’ Chirano Goldmine has gone from 24 to 4 service shutdowns per year on each of their Volvo mining trucks. For their entire fleet this equals 800 less service intervals per year, 9 major overhauls eliminated per year, or 681,000 USD in annual savings on their fleet of 40 trucks.
How is this possible?
Because they are using technology which has successfully kept wind turbines in operation without breakdowns and only one annual service interval for decades. Ten years ago, this was unknown in the mining industry; today it is standard equipment on new Sandvik and Metso crushers. The solution is in-depth CJC® Offline Oil Filtration.
What to obtain
Despite how dirty and tough the operating conditions are, mining companies are able to
- save 50 – 75% of their oil consumption
- eliminate three out of four shutdowns of equipment
- reduce running costs by around 50 – 60%
by implementing CJC® Offline oil filtration because it ensures much cleaner and less stress full operating conditions for gearboxes, bearings, hydraulic systems – for any oil system; and in the mining industry these are everywhere.
Learn from other mine sites' experiences with the benefits from maintaining their system oil clean: