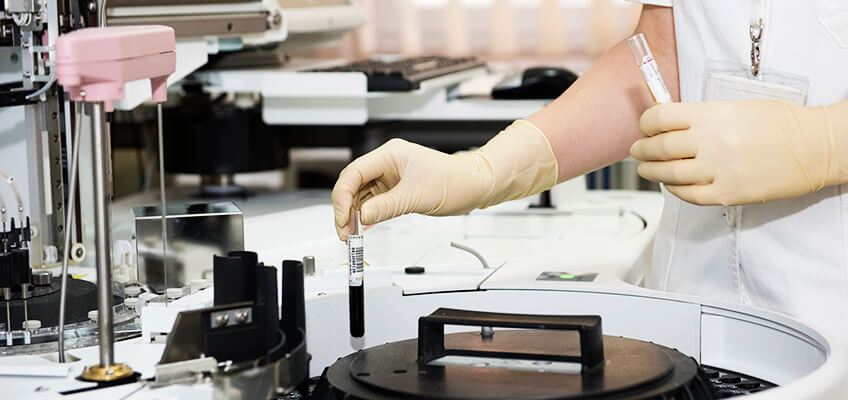
oil analysis
Information about the oil's properties and its wear and tear on the system is important for preventative maintenance and to ensure optimal operations.
The right type of oil analysis can say something about the state of the system and life expectancy of the oil. Typically, the primary sources of contamination of oil systems are particles, oxidation and water.
To select the correct analyses, it is important to consider the type of oil and application.
At a minimum, an oil analysis should include:
- Gear and hydraulic oils: viscosity, total acid number (TAN), water content in ppm and particle count (ISO 4406).
- Turbine oils (gas, steam and water turbines): viscosity, acid number (TAN) and oxidation level (MPC test).
- Engine lubricating oils: viscosity, total base number (TBN), water content and particle/soot content using insoluble residue in n-pentane (membrane or centrifuge test).
- Transformer oils: dissolved gases, water content in ppm, acid number (TAN), dielectric strength.
- Diesel: water content in ppm, microorganisms and particle count (ISO 4406).
If you want to know more about the system and the state of the oil, or if there are special reasons for further studies, the following analyses may be relevant:
- Elemental analyses (ICP/RDE): wear particles, additives, contamination in ppm.
- Membrane filtration: weight of deposits on membrane.
- Membrane filtration: microscopy/photos of particles on membrane.
- Particle counting: comparison of counting by laser and microscope.
- Demulsification: determination of the oil's ability to separate water.
- Mini-desorber test: the ability of the oil to separate water by the principle of desorption (internal test).
- Flash point: on suspicion of decomposed oil or mixed diesel e.g. engine oil.
- MPC (Membrane Patch Colorimetry) test: membrane oxidation residues, e.g. turbine oil and hydraulics.
- FTIR (Fourier-transformed infrared spectroscopy) can show the difference between new and used oil, e.g. oxidation, soot, additives, cross-contamination.
- Interface and surface tension can show the general state of the oil. Good test, e.g. transformer oil
- Insoluble residue in n-pentane/toluene, centrifuge test.
- RPVOT: can show the oil's ability to withstand oxidation measured over time. Estimates the active antioxidant content, compared to new oil.
- RULER test: tests content of amines/phenols compared to new oil (antioxidants).
- Foaming tendency test according to ASTM sequence I-III.
- Flender foaming test for gears.
- PQ index: shows the amount of magnetic wear particles in the oil.
- Inspection of used filter components.
C.C. JENSEN has developed a method for examining used CJC® Filter Inserts, which provides an image of the type of particles retained in the CJC® Filter Insert. Deposits on the surface of the used CJC® Filter Inserts, surface scrapings of the CJC® Filter Inserts, as well as membrane analyses are investigated. The report contains photos from the microscope of the types of particles found.
C.C. JENSEN's laboratory in Svendborg performs analyses in accordance with ISO/ASTM standards and internal methods developed to support the products/solutions provided by C.C. JENSEN. In addition, we cooperate with independent external laboratories in Europe.
Our subsidiaries use both the laboratory in Svendborg and local laboratories globally.
This makes it possible to perform both routine and special analyses in cooperation with C.C. JENSEN.
Please read section 3 of our Clean Oil Guide.